Optimizing Wire Production with a Black Annealing Furnace in a Binding Wire Factory
In the bustling world of binding wire factories, the quest for enhanced productivity and superior wire quality is an ongoing pursuit. At the heart of this endeavor lies the black annealing furnace, a crucial piece of equipment that plays a significant role in determining the strength and flexibility of the finished product. This article delves into the importance of utilizing a black annealing furnace within the production process of a binding wire factory.
The black annealing furnace operates under the principle of heat treatment to modify the physical and sometimes chemical properties of metals. In the context of a binding wire factory, it serves to soften the metal wire by reducing its hardness and increasing its ductility. This process is essential because it allows the wire to be drawn through smaller dies without breaking, which results in finer gauge wires that are more suitable for binding applications.
During the annealing process, the wire is heated to a specific temperature and then cooled under controlled conditions. The black annealing furnace gets its name from the surface oxidation that occurs on the wire during heating, giving it a darkened appearance. This layer of oxide actually serves a protective function, preventing further corrosion and preserving the integrity of the wire's surface.
For a binding wire factory, investing in a high-performance black annealing furnace can lead to numerous benefits
For a binding wire factory, investing in a high-performance black annealing furnace can lead to numerous benefits
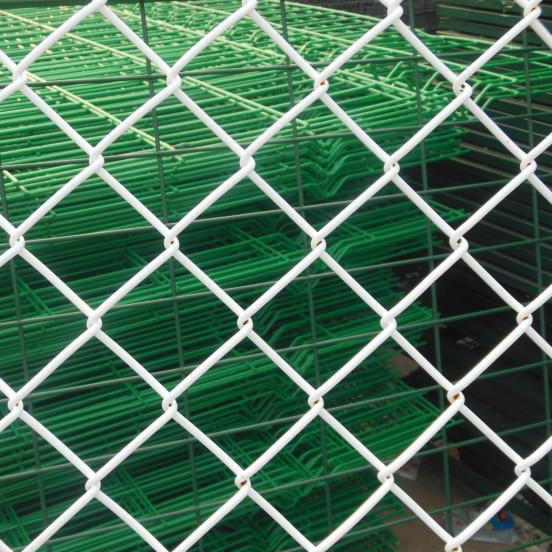
For a binding wire factory, investing in a high-performance black annealing furnace can lead to numerous benefits
For a binding wire factory, investing in a high-performance black annealing furnace can lead to numerous benefits
black annealing furnace for binding wire factory. Firstly, it ensures consistency in the quality of the wire produced, as the even heating and cooling provided by the furnace result in uniform material properties across the entire length of wire. Additionally, the increased ductility means that there is less waste due to breakage during the drawing process, which can significantly reduce material costs.
Moreover, the use of a black annealing furnace contributes to energy efficiency within the factory. Modern furnaces are designed with advanced heating elements and insulation technologies that minimize heat loss, thus reducing energy consumption. This not only lowers operational expenses but also aligns the factory's practices with sustainable manufacturing principles.
In conclusion, the integration of a black annealing furnace into the production workflow of a binding wire factory is indispensable. It refines the wire's characteristics, enhances production efficiency, and ensures that the end product meets the rigorous demands of the industry. As technology continues to advance, so too will the capabilities of these furnaces, promising even greater improvements in wire quality and manufacturing sustainability for binding wire factories worldwide.