Ensuring the longevity and structural integrity in a variety of applications starts with selecting the right materials; one such material gaining notable traction in industries worldwide is OEM galvanized binding wire. This robust material is defined by its unique characteristics that cater to diverse needs across construction, industrial, agricultural, and even everyday household use.
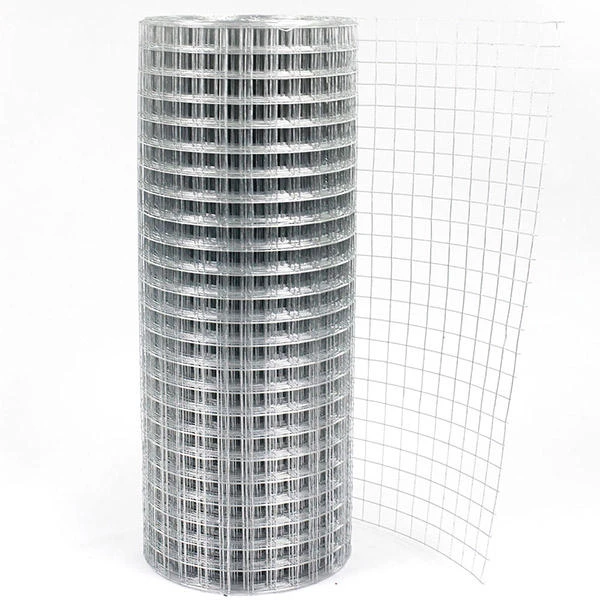
Galvanized binding wire, as the name suggests, is steel wire coated with a layer of zinc to enhance its durability against rust and corrosion. The term OEM (Original Equipment Manufacturer) implies that these wires are specifically engineered to meet high performance and quality standards set by manufacturers who produce their own components and products. This strategic move aligns with specific business requirements, ensuring reliability, uniformity, and enhanced performance.
Experience with OEM Galvanized Binding Wire
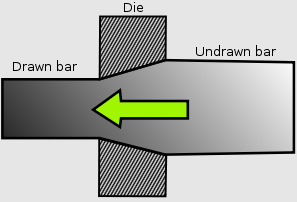
From the expertise gathered across various industries, the practical experiences with OEM galvanized binding wire showcase its extensive benefits. In the construction sector, for instance, the wire’s ability to withstand harsh environmental conditions makes it indispensable. Contractors prefer it for securing scaffolding, rebar in concrete settings, and other structural parts because it resists rust far better than bare steel wire, leading to significantly longer life and reduced maintenance costs.
In agriculture, the wire’s robust nature offers unparalleled utility. Farmers and agricultural businesses utilize OEM galvanized binding wire extensively for bundling harvested crops, constructing fences, and maintaining animal enclosures. Its corrosion resistance is crucial in environments that are often wet or exposed to the elements, ensuring the wire does not weaken over time, which could compromise crop transport or animal safety.
Expertise in Manufacturing
The production of OEM galvanized binding wire involves advanced technological processes that guarantee high tensile strength while maintaining flexibility. Manufacturers apply the hot-dip galvanization process, where steel wires are submerged in molten zinc. This creates a thick, tightly adherent zinc coating that serves as a formidable barrier to corrosive elements.
Technical experts favor using high-quality raw materials and stringent quality assurance protocols to ensure that each batch of wire meets industry standards. The precision exercise in the diameter and coating thickness significantly affects the product’s performance, thus understanding these details is vital for anyone involved in purchasing or specifying materials for projects.
oem galvanized binding wire
Authoritativeness in Usage
OEM galvanized binding wire emerges as an authoritative material due to its ubiquitous application and dependency across various sectors. It embodies the mainstay of binding solutions by offering consistent performance and reliability. Companies spearheading major projects often rely on this wire to meet project specifications and safety standards.
Their trust in its performance underscores the role of galvanized binding wire in maintaining structural integrity and safety.
In the realm of DIY projects or small home applications, homeowners and craftsmen favor these wires for their ease of use and reliability. Whether it is for tying up plants in the garden or improvising small repairs around the home, the wire's adaptability is unmatched. Given its wide availability and adaptability, OEM galvanized binding wire becomes a primary choice for users seeking a balance between performance and cost-effectiveness.
Trustworthiness and Safety
The trustworthiness of OEM galvanized binding wire is rooted in its proven track record across industries. Quality assurance tests, which verify properties such as zinc coating thickness and tensile strength, provide assurance that each wire coil adheres to rigorous safety standards. This commitment to quality helps prevent failures that could lead to infrastructural or mechanical hazards.
Furthermore, educational initiatives by manufacturers play a crucial role in enhancing user safety and awareness. By providing guidelines on proper handling, storage, and application, manufacturers ensure that end-users maximize the potential of their products without compromising safety.
In conclusion, OEM galvanized binding wire stands out as an essential product that deepens its importance with each successful application. Combining expertise in manufacturing with practical applications and unwavering reliability, this wire type not only meets but exceeds the expectations of those seeking durable and versatile solutions. As industries continue to evolve, the pivotal role of such materials in innovative and sustainable projects remains undiminished—cementing galvanized binding wire as an indispensable part of the modern industrial fabric.