Crafting high-quality hot dipped galvanized steel grating demands more than mere expertise; it requires a nuanced understanding of both the process and the end-use applications. Having contributed extensively to the field of steel fabrication over several decades, it is clear that the foundation of reliable hot dipped galvanized steel grating begins with sourcing premium raw materials. The choice of steel is critical, as it must possess the requisite tensile strength and durability to withstand subsequent processing stages. Only by rigorously testing each batch of steel for qualities like carbon content and structural integrity can manufacturers ensure a robust final product.
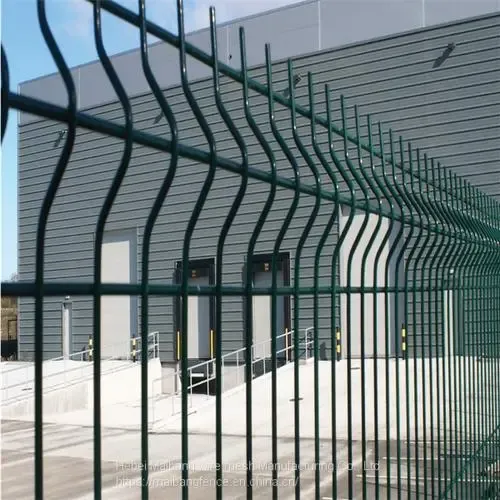
The hot dip galvanizing process itself is a symphony of science and precision. It begins with the meticulous cleaning of the steel through a series of chemical baths to remove all impurities, such as dirt, oil, and mill scale, which could impede the galvanizing bond. Following this, the steel is immersed in a molten zinc bath at approximately 450°C (842°F). This immersion forms a robust metallurgical bond between the zinc and the steel substrate, resulting in a uniformly coated surface with exceptional resistance to corrosion.
Expertise in the galvanizing process extends beyond the mechanics to include an appreciation of zinc’s natural properties. The zinc layer is not merely a coating but an active barrier. It provides cathodic protection, meaning that the zinc sacrifices itself to prevent corrosion of the underlying steel, thus prolonging the life and durability of the grating even in the harshest of environments. This characteristic is crucial for applications ranging from industrial flooring to offshore platforms, where safety is paramount.
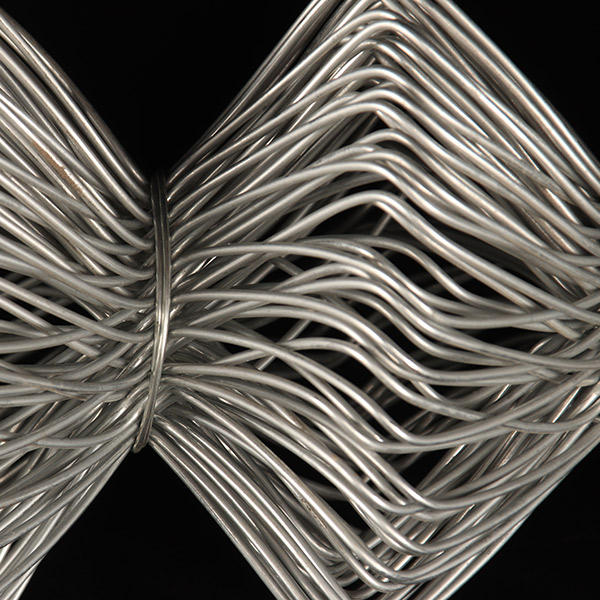
From experience in real-world applications, choosing the correct type of grating for specific uses can enhance both performance and safety. For instance, bearing bar grating provides the necessary strength for flooring in factories and plants, while serrated grating is preferred in areas prone to spills, reducing the risk of slips and falls. Understanding these subtleties enables manufacturers to guide customers in selecting the optimal grating type for their requirements.
produce hot dipped galvanized steel grating
Industry leadership is not just about product excellence but also about earning client trust through transparency and communication. Providing comprehensive specifications for each grating product, including load-bearing capacities and compliance with international standards like ANSI and OSHA, assures clients of the grating’s suitability for their specific applications. Furthermore, by maintaining rigorous quality controls through every phase of production, from raw steel procurement to final inspection, trust in the reliability and safety of the end-product is fostered.
Manufacturers committed to sustainability and environmental stewardship also enhance their credibility. By ensuring that zinc used in the galvanizing process is responsibly sourced and recycled, and minimizing waste through efficient manufacturing processes, producers can appeal to environmentally-conscious clients and contribute positively to the global aim of reducing industrial footprints.
In conclusion,
the creation of hot dipped galvanized steel grating is an intricate dance of science, engineering, and practical application. Those who excel in this domain do not only master the technical elements but also embrace the responsibility of producing safe, durable, and sustainable products. A reputation for excellence in this area cements a manufacturer's standing as a trusted leader in the steel fabrication industry.