In the realm of industrial applications and construction, selecting the right materials can be a crucial decision that impacts both the quality and longevity of a project.
One such material that has gained prominence is OEM hot dipped galvanized iron wire. Known for its superior durability and corrosion resistance, this wire is a preferred choice for a variety of applications, from fencing to creating meshes and intricate crafts.
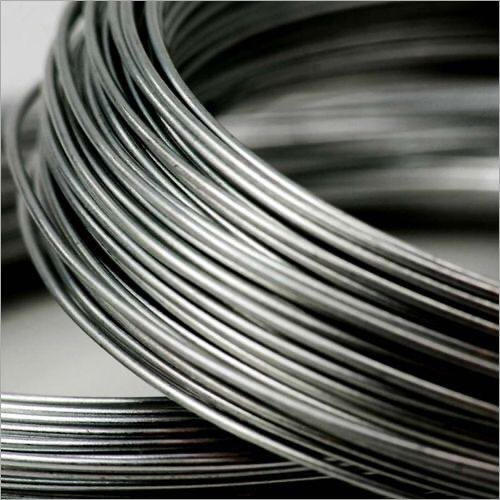
Hot dipped galvanization is a process that enhances the resistance of iron or steel, offering a protective layer by immersing the base material in molten zinc. This technique has stood the test of time, providing substantial protection against rust and environmental wear. Over decades, industries across different sectors, ranging from agriculture to construction, have leveraged this process for both its economic and durable qualities.
The expertise imbibed in OEM hot dipped galvanized iron wire results from a meticulous manufacturing process that adheres to stringent quality standards. Producers often initiate the process by selecting high-grade raw iron, ensuring that the base material meets necessary specifications for tensile strength and elasticity. Through the galvanization process, the zinc coating uniformly covers the wire, ensuring an even distribution that prevents moisture penetration and enhances its life span.
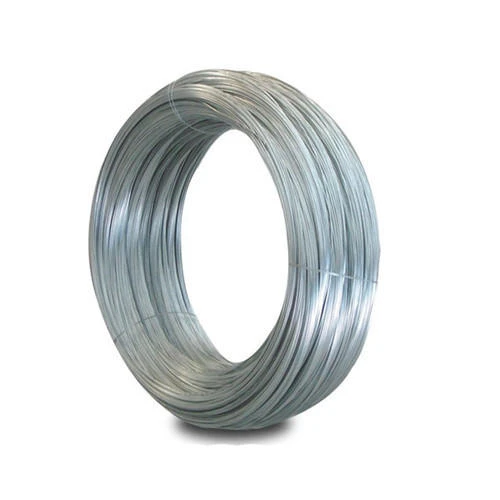
When considering applications where environmental conditions can be harsh, such as coastal regions where salt in the air accelerates corrosion, or industrial settings with high levels of humidity or chemical exposure, OEM galvanized wire demonstrates superior performance. Its rust-resistant properties ensure that it maintains structural integrity, reducing the need for frequent replacements and thus optimizing overall project costs.
oem hot dipped galvanized iron wire
The authority of hot dipped galvanized wire also extends beyond merely its physical properties. Its adaptability makes it a versatile component in a myriad of projects. In the agricultural sector, for example, it finds usage in constructing durable and long-lasting fencing solutions, ensuring livestock safety while standing up to environmental challenges. Urban planners and civil engineers regard this wire as indispensable when designing urban landscapes and public infrastructures, whether it’s in the form of secure barriers or lasting utility installations.
Additionally, the growing trend of DIY projects and custom manufacturing has further propelled the demand for OEM hot dipped galvanized wire. With the increase in creative applications, from artistic sculptures to bespoke outdoor installations, its usage underscores a balance between aesthetic appeal and functional reliability.
Trustworthiness in the use of this material is established through rigorous industry testing. Standards and certifications from international bodies like ISO and ASTM ascertain that the production processes meet global safety and quality standards. Moreover, the manufacturers often provide certifications that verify the compliance of the wire with these international standards, adding an extra layer of assurance to buyers and contractors about the product’s capabilities.
In summary, OEM hot dipped galvanized iron wire stands as a paragon of quality and durability in construction and multiple industrial sectors. Its comprehensive benefits—from enhanced protection against corrosion to the robustness and adaptability across diverse environments—are testament to its indispensability. The collaborative synergy of experience, expertise, authority, and trust that underpins its manufacture ensures that it remains a cornerstone material for future projects requiring reliability and economic efficiency. As industries continue to evolve, the demand and application of such time-tested materials will undoubtedly continue to expand, meeting the needs of a modern, interconnected world.