In the dynamic realm of construction and industrial applications, OEM hot dip galvanized steel grating stands out as a cornerstone material that offers an unparalleled combination of strength, longevity, and versatility. This article delves into this essential product, highlighting why it has garnered trust and authority among industry professionals.
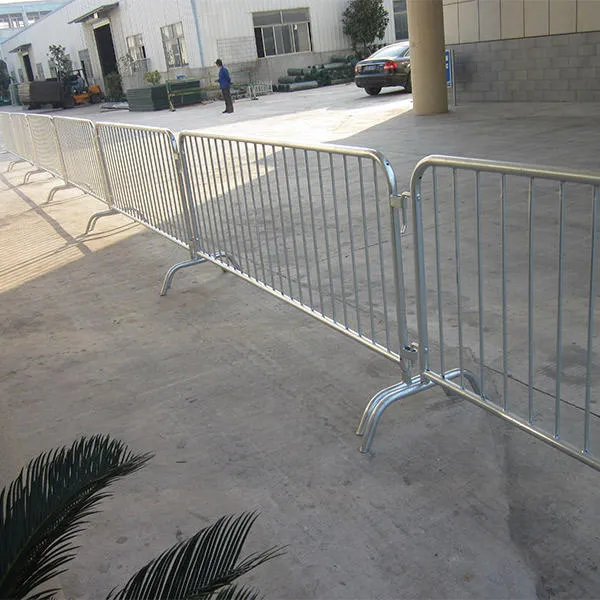
Steel grating, especially when enhanced with a hot dip galvanized finish, offers outstanding performance in diverse environments. The galvanization process involves dipping the fabricated steel grating into molten zinc, which forms a robust layer of zinc-iron alloy. This not only provides a strong barrier against corrosion but also enhances the grating's visual appeal, making it suitable for open and visible architectural projects as well as robust industrial uses.
The expertise applied in the manufacture of OEM hot dip galvanized steel grating sets a benchmark in high-quality applications. Produced through precise processes, these gratings are used in the construction of platforms, walkways, and stair treads across industries. Engineers and architects favor this material due to its load-bearing capacity, which is essential for ensuring safety and durability in industrial infrastructures. The integration of stringent quality checks at each stage of production guarantees that each grating piece meets international safety and quality standards.
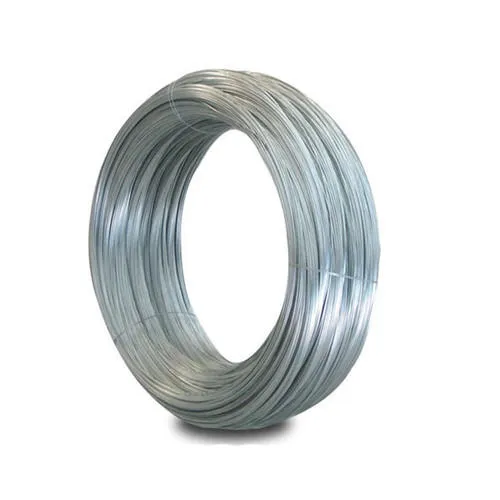
Real-world experience with these grates confirms their superiority. For instance, marine and coastal industries, which are notoriously harsh due to constant salt exposure, have noted a marked improvement in structure longevity where hot dip galvanized grates are employed. This is credited to their excellent corrosion resistance, even when subject to unfavorable weather conditions.
Moreover,
the adaptability of OEM hot dip galvanized steel grating cannot be overstated. They can be customized to fit various specifications, from the thickness and spacing of the bars to the size and dimension of the entire sheet, allowing for applications that range from heavy industrial use to decorative architectural projects.
oem hot dip galvanized steel grating
Trustworthiness is central to the widespread adoption of this product. Many top-tier construction companies and industrial plants specify OEM hot dip galvanized steel grating in their projects, a testament to their reliability. Certification from respected industry standards bodies further reinforces this trust, ensuring that the materials used adhere to safety regulations and performance expectations.
These gratings also offer an eco-friendly solution. Steel is a material that can be recycled multiple times without losing its properties, aligning with the sustainability goals of modern enterprises. The galvanization process also extends the life of the grating, reducing waste and the frequency of replacements needed, thus supporting both economic and environmental efficiency.
Additionally, the ease of installation of these gratings is noteworthy. Their design facilitates quick assembly and maintenance, reducing downtime during construction and ensuring efficient completion of projects. This efficiency is critical in industries where time equals money, and delays can have significant financial implications.
Ultimately, OEM hot dip galvanized steel grating represents a synthesis of durability, reliability, and versatility. Its application across various demanding settings—whether for protecting workers at height in industrial plants or providing a corrosion-resistant platform in coastal areas—showcases a product that is not only essential but exemplary. As industry demands continue to evolve, the steadfast performance of these gratings ensures they will remain at the forefront of material selection for architects and engineers worldwide.